The Dos and Don’ts of Industrial Wire Marking
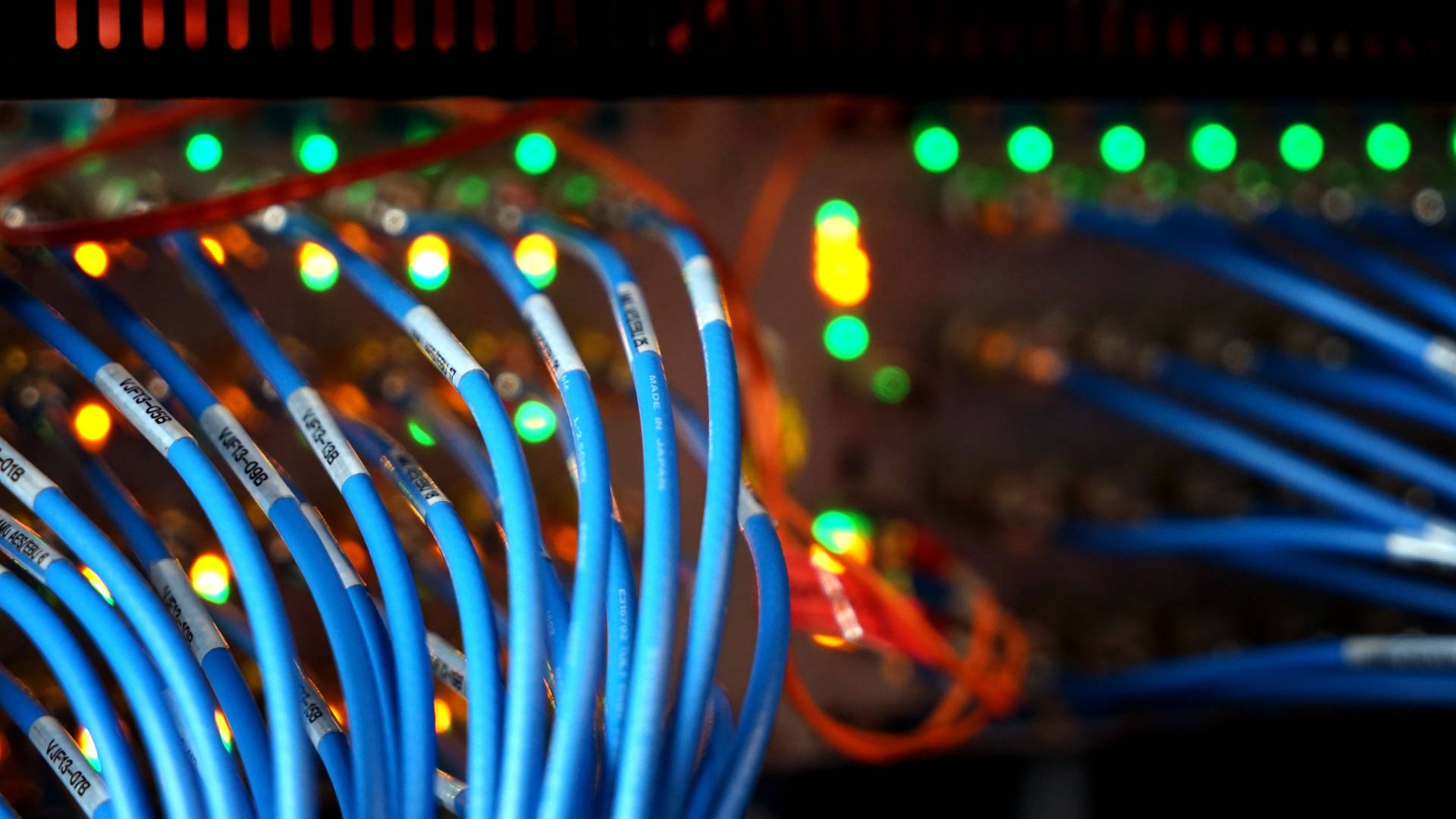
When it comes to industrial settings, correct wire marking can mean the difference between operational efficiency and potential hazards. While it might seem like a small detail, wire marking plays a pivotal role in maintaining safety, compliance, and seamless functionality in complex electrical systems. We’ll break down some of the important dos and don’ts of industrial wire marking that industrial managers and electrical engineers should always remember.
The Dos of Industrial Wire Marking
When it comes to industrial wire marking, the quality of the materials, the labeling system, and maintenance are critical to operational safety and efficiency.
Invest in High-Quality Labeling Materials
First and foremost, invest in high-quality labeling materials. Durable labels that can withstand harsh industrial conditions—such as extreme temperatures, moisture, and chemicals—are crucial.
Opt for labels and labeling processes that are resistant to fading, smudging, and peeling. This ensures that markings remain legible over time, facilitating easy identification and maintenance.
Standardize Your Labeling System
Consistency is key in wire marking. Use a uniform color-coding scheme and clear, readable fonts to ensure there’s no discrepancy in wire marking throughout the system or facility.
Each label should provide essential information, such as wire function, voltage rating, and destination. Standardization simplifies identification and reduces the risk of errors, especially when multiple personnel handle the wiring.
Regularly Update and Maintain Wire Markings
To ensure continuity and durability, electrical engineers should regularly update and maintain their wire markings and labels. Industrial environments are dynamic, with frequent changes and upgrades.
Ensure the wire labels reflect any modifications to the wiring system. Conduct periodic reviews to check the condition of existing labels and replace any that are worn or damaged.
The Don’ts of Industrial Wire Marking
Now that we’ve covered the dos of industrial wire marking, there are many don’ts that industrial managers and electrical engineers should strive to avoid.
Overlook Label Placement
Neglecting the correct placement of labels can lead to confusion and safety hazards. Position wire markings and labels where they are easily visible and accessible. Proper placement is crucial for compliance and helps prevent costly mistakes in industrial settings.
Neglect Training
Do not overlook the importance of proper training. Ensure that all personnel involved in wire marking are adequately trained in the standardized labeling system.
Mislabeling or inconsistent application of labels can lead to confusion and errors, particularly in emergencies. Comprehensive training ensures that everyone understands and adheres to the established wire marking protocols.
Forget or Ignore Regulatory Requirements
There are many specific wire marking standards you should know about that govern industrial wire marking and particular industries. Non-compliance can result in severe consequences, including fines and operational shutdowns. Stay informed about the relevant guidelines and ensure that your wire marking practices align with them.
Conclusion
There are many considerations in industrial wire marking; if you prioritize these important rules, we’re sure you’ll end up with a compliant, efficient, and highly functional industrial wire marking system. Continuous improvement and regular updates are key to maintaining the integrity of your wire marking system. Invest in quality, prioritize training, and stay compliant to unlock the full potential of your industrial operations.