Tank test tanked, Positive test leads to water chlorination
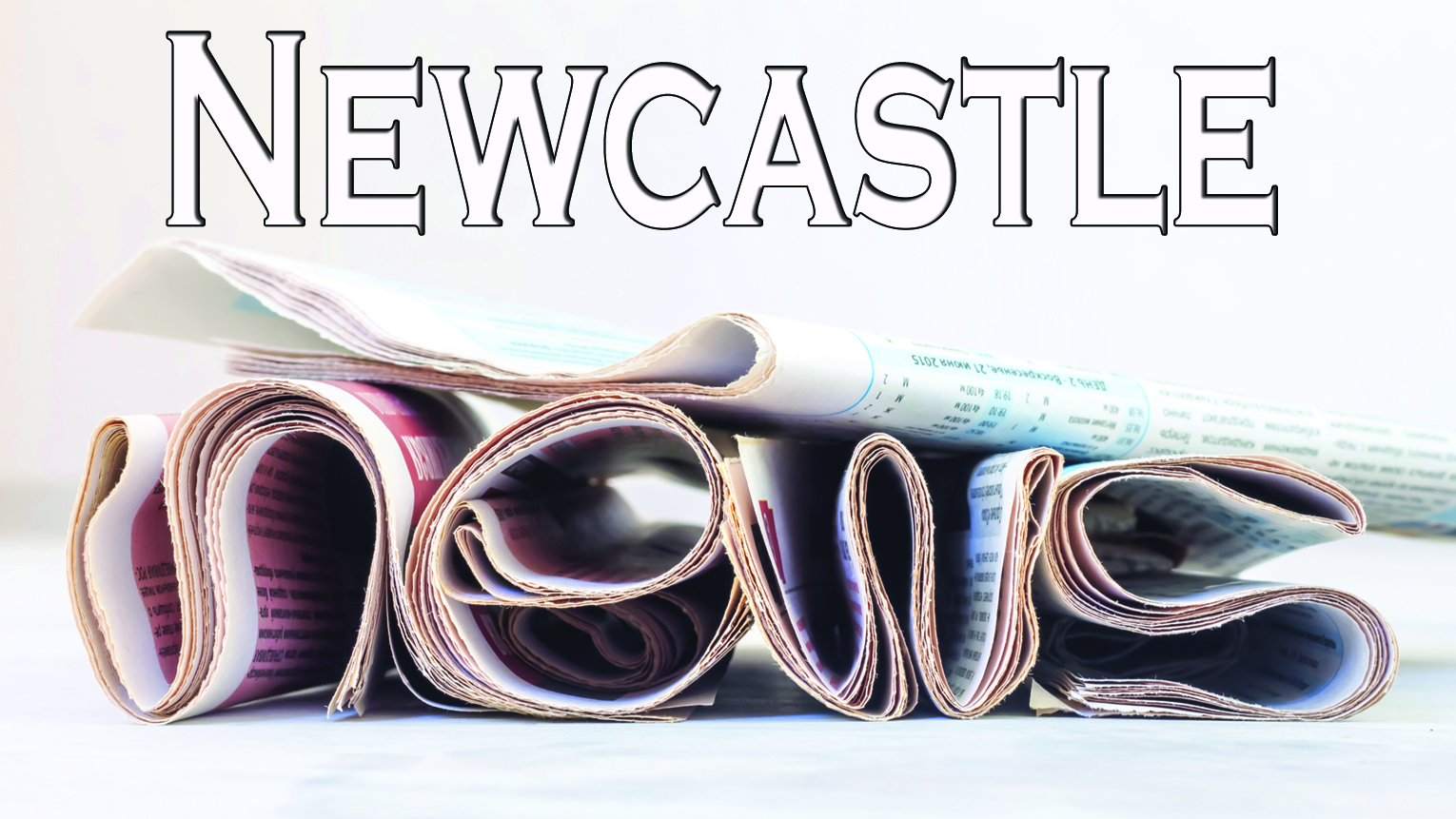
Citizens were left frustrated and expressing frustrations on Facebook after the city chlorinated Tank No. 1 to disinfect the water in response to samples testing positive for bacteria in October.
Purchased from a company in Glendo in 1934, Tank No. 1 was disassembled and reassembled in Newcastle between 1934 and 1935, Greg Stumpff, public works supervisor said. So the tank has been servicing Newcastle for 90 years.
According to Stumpff, Tank No. 1 services a majority of town. The only area the tank doesn’t provide water to is the avenues, he noted.
“Unfortunately, with an older system and an older tank, there are issues,” he said.
According to Stumpff, routine testing revealed samples that were positive for total coliform (TC) and negative for E. coli coliform (EC).
All required repeat samples were positive for TC and negative for EC as well, he noted.
The city was then required to collect samples from all water wells, which, Stumpff said, came back negative for both TC and EC.
“We contacted Region 8 EPA (Environmental Protection Agency) which is our regulating agency for water sampling, and we were required to complete Level 1 and 2 assessments to find the source of the issue,” Stumpff said in an email. “Since our GWR well samples were all negative we knew the issue was between the wells and the first TC positive sample site on Sumner Ave.”
To help diagnose the issue, he said, another set of special samples were collected in the distribution system between the wells and Sumner Avenue.
“While we were waiting for the special sample results, we began checking any area that bacteria could enter the distribution system. When we received the results of the special samples, they demonstrated we had an issue starting at Tank No. 1 (the tan tank just north of E. Wentworth Street on U.S. Highway 85), which is a hot riveted steel tank built in 1934,” Stumpff said in the email.
With a closed system, he said that repair work on wells and pump stations was the only way bacteria would be allowed into the system, and with no recent maintenance, the city investigated further.
Upon examining Tank No.1 more closely, city crews discovered that since the previous month’s inspection, the vent screen top clamp had broken and was missing, Stumpff said. The screen was found pulled away from the vent.
“With this finding and not knowing what could have entered Tank No. 1 we chlorinated the water tanks and began checking chlorine residuals immediately after. Our target chlorine level for such an incident is 1 part per million (ppm). The EPA has set the Maximum Contaminant Level (MCL) for chlorine at 4 ppm,” Stumpff said in the email. “During checking chlorine residuals twice daily for 5 days we never exceeded 1 ppm.”
He noted that the screen was replaced and new clamps were also installed on the tank.
According to Stumpff, the positive sample would usually be attributed to an animal entering the tank, but because the results were EC negative and TC positive, they do not suspect an animal is the cause.
“We also called a specialized company licensed to clean and inspect Tank No. 1 for any sort of foreign debris that might have caused the issue. The company did not find any definitive substance or issue,” he said in the email. “We did clean the tank anyway during the inspection.”
After the chlorine levels dropped below 0.1 ppm, Stumpff said, further testing was completed on Nov. 4 and 5 with both sets of samples coming back negative for both TC and EC, indicating the bacteriological issue has been addressed.
The next step, according to Stumpff, was the Level 2 assessment.
This assessment is not performed by the city and must be performed by either EPA staff or a contractor hired by the EPA to investigate. The purpose of the assessment is to investigate the findings of the Level 1 assessment and to have outside personnel look at the city’s system.
“On Oct. 28 and 29, we met with Region 8 EPA representatives to complete a Level 2 assessment. We only have their preliminary report and not the final report. We are waiting on the final report and what corrective actions EPA will require,” Stumpff said.
Tank No.1 is scheduled for replacement on the capital improvements plan in 2028, according to Stumpff. The projected cost of the project is in excess of $9 million.
This, he said, is because of several issues detected during a 2013 project.
“There was a poor repair all the way around a portion of the wall of the tank for an unknown reason. Also, during this maintenance project, we found a thick coat of fiberglass coating on the floor which is not normal,” Stumpff said in the email. “After removing this coating, we found the steel floor of the tank had multiple holes. We contracted a welder to patch the tank and the contractor welded 404 patches on the floor of the tank. During this project we also separated the inlet and outlet of the tank to improve circulation in the tank and improve water quality in the tank.”