Electrical Safety Advice for Industrial Cold Saw Machines
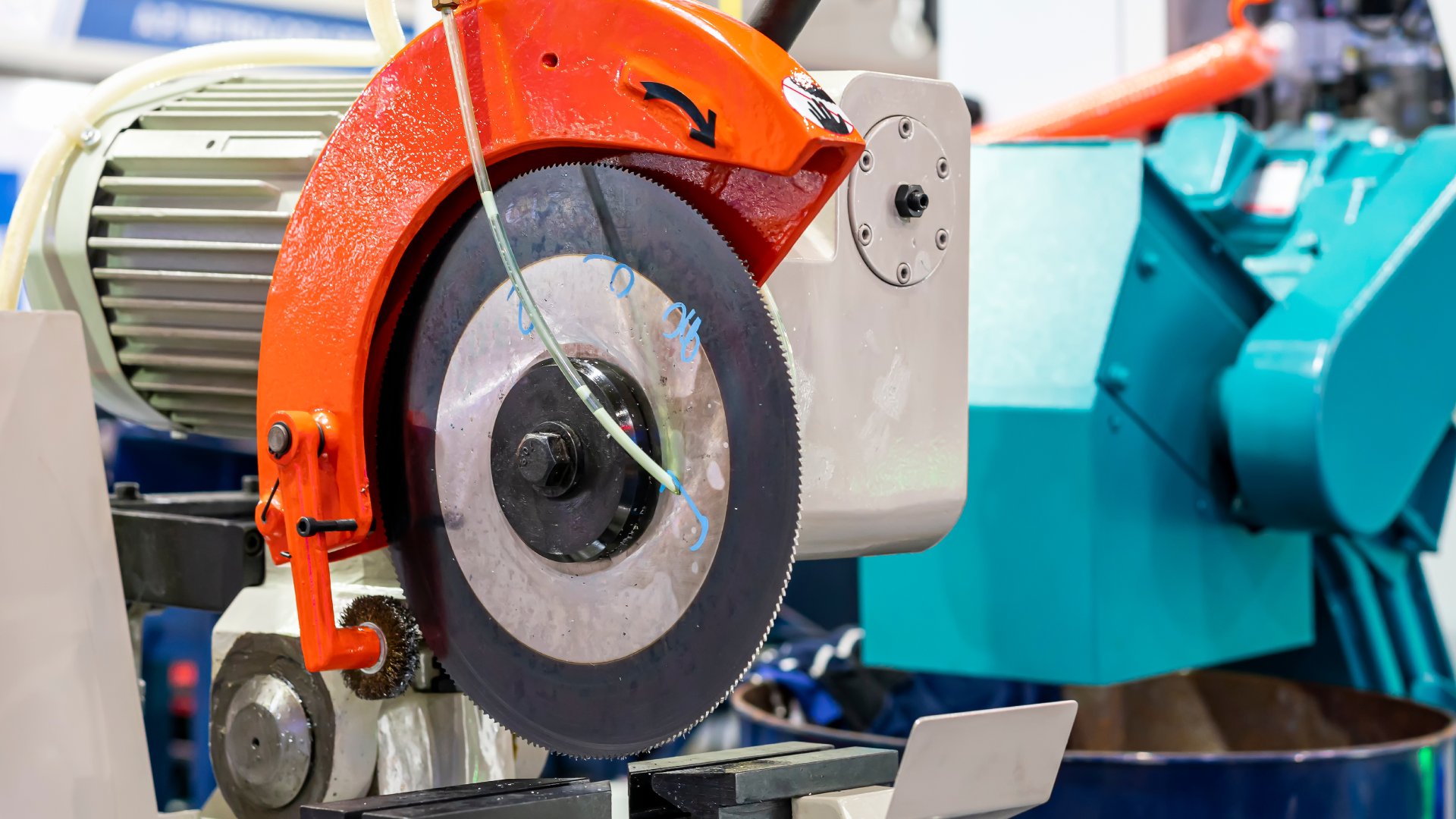
Electrical safety is a critical aspect of operating industrial machinery, and cold saw machines are no exception. These powerful tools play a vital role in metal fabrication and cutting, but improper handling of their electrical systems can lead to serious accidents and even fatalities.
By understanding the potential hazards and following safety practices, operators and safety officers can secure a safer working environment for everyone. Below, we’re taking an inside look at the best electrical safety advice for industrial cold saw machines and why you should follow these best practices.
Understanding Electrical Systems in Cold Saw Machines
Cold saw machines are precision-engineered tools equipped with electric motors, control panels, and power supplies to enable accurate metal cuts. These systems run on high electrical power, making them susceptible to issues, such as short circuits, wiring malfunctions, or overloads.
Recognizing the complexity and risks associated with their electrical components is the first step to maintaining a safe work environment. Familiarizing operators with the electrical layout and providing training are essential measures to mitigate potential dangers.
Identifying Common Electrical Hazards
Electrical hazards in cold saw machines primarily stem from faulty wiring, poor insulation, or damaged components. Frayed cables and exposed wires can cause shocks while improper machine grounding increases the risk of electrical fires. Water or moisture near electrical connections can further amplify the likelihood of accidents.
Regular inspections are fundamental to identifying such hazards early. Operators must remain vigilant about unusual smells, sparks, or sounds emanating from the machine, as these may indicate underlying electrical issues requiring immediate attention.
Preventing Electrical Accidents With Best Practices
Preventing electrical accidents begins with proper training and adherence to safety protocols. Always check that the cold saw is connected to a power supply that meets the manufacturer’s specifications.
Operators must avoid handling electrical equipment with wet hands or near water, as moisture is a leading cause of electrical malfunctions. Additionally, wearing appropriate personal protective equipment (PPE), such as rubber gloves and insulated footwear, can minimize the risks of shocks during operation.
Implementing lockout/tagout (LOTO) procedures is another best practice for preventing accidental energization of the cold saw during maintenance or repair. These protocols guarantee that only authorized personnel manage the machine while it is undergoing work.
The Impact of Regular Maintenance on Safety
Proper maintenance is key to ensuring the electrical safety of cold saw machines. Scheduled check-ups should include inspection and testing of electrical components, such as cords, plugs, and switches. Any defects or wear-and-tear identified during maintenance must be addressed immediately to prevent equipment failure.
Keeping the machine clean and free from debris also prevents dust and metal particles from damaging electrical systems. For more comprehensive advice, be sure to read through the guide to maintaining your cold saw, as it provides valuable insights into keeping your equipment in optimal condition.
Electrical safety for cold saw machines is not optional. By identifying hazards, implementing preventative measures, and emphasizing regular maintenance, industrial teams will create secure environments for machine operators. Take proactive steps to ensure the safety of your team and equipment today.